使っている道具を見れば,職人の腕は大体分かる.
皆さんもこんなエピソードを聞いたことがおありだろう.
左甚五郎が修行の旅の途上で初めて会った親方にかんながけを命じられる.
甚五郎は半日かけてかんなを研ぎ,二枚の板にかんなをかけた.仕事の遅さを笑う職人たちの目の前で,この二枚の板に口に含んだ水をぷっと吹きかけ張り合わせるとぴたりと張り付きなまじの力でははがせなかったという.
先日お邪魔した工場で工具を見せていただいた.ペンチを金槌代わりに使ったのであろう,打痕がそこいらじゅうについており変形している.
こういう工場ではよい仕事は期待できない.
道具に感謝し丁寧に使う.
そして道具や設備に工夫を凝らす.買って来た設備はそのまま使わない.使いやすいように工夫する.
日本のモノ造りのすばらしさは,物を作る道具を作れることである.
古い生産設備をぴかぴかに磨き上げ,且つ自分たちの工夫を入れ込んである.
こういう工場は見掛けは悪くても,モノ造りの心が伝わってくる.
使っている設備を見れば,工場の現場力は大体分かる.
「品質保証」カテゴリーアーカイブ
妥協しないモノ造りは妥協しないヒト造り
毎月「品質改善・経営革新セミナー」を開催している.セミナーにご参加いただいた経営者様,工場管理者の皆様からいろいろなお話を聞き,大いに勉強になっている.
以前ご参加いただいた中国縫製工場の管理者様は,ウチの幹部は現場上がりの人が多く,小学校しか卒業していない人が多い.そういうメンバーに新しいことをさせようとすると尻込みしてしまう.と言うお悩みをうかがった.
また別のアパレル系検品工場を経営されている方からは,ベテラン作業者を監督職に昇格させようとすると,字の読み書きが出来ないからと辞退されてしまうと言うお話も聞いた事がある.
皆さん中国の工場では,日本では想像が付かないようなご苦労をされてる.
しかしこういう状況を良く考えてみると,これもひとつの強みに転換できるのではないかと考えている.中学もろくに卒業していない農村出身の作業者が何年も勤めてくれて,ベテラン作業者になっている.こういう人たちはなかなか転職して行かない.
事実,この検品工場は4%以下と言う非常に低い離職率だ.日本の製造業と比較してもかなり低い数字ではないかと思われる.
こういう作業者達に少しずつ能力を付けてゆけば,時間はかかるが優秀な現場リーダに育てる事が出来る.
「妥協しないモノ造りは妥協しない人造り」である.
誤出荷
以前中国の生産委託工場から出荷した製品の中に違う機種が一台混ざっていたというクレームをお客様からいただいた事がある.
クレーム品を調べてみると,製品そのものは同じだがラベル銘版を別機種の物を貼って出荷してしまった事が判明.全く同じ製品なのだが,お客様が仕向け地別に型名の枝番号を変えているので,ラベル違いで3機種ある.ラベルも型名の最後の二桁が違うだけで殆ど同じである.
したがってラベルを貼り間違えてしまう可能性は,生産開始時点から予測していた.
そのため型番ごとに作業指示書を3セット用意し,ラベル貼り作業,目視検査工程の作業指示書にはラベル現物を表示した.
それでも問題は発生した.
工程の記録によると,内部異物(ケースを振るところころ音がする)不良でラインアウトした物がある.この場合超音波融着してあるプラスチックケースを開けて,中の異物を確認・除去しなければならない.従ってケースは再利用できず交換することになる.ラベルも新たに貼らねばならない.
通常であれば修理完了後ライン復帰しラベル貼り工程,目視検査工程を通るので,不良は発生しないはずである.
更に班長の記憶を調査してみると,修理品のライン復帰時に既に別の機種を生産しており,別の機種が流れているラインで班長が持ち回りで,検査梱包工程を通した事が判明.
このときに班長が作業者に間違ったラベルを渡し,目視検査員も見逃してしまった,というのが真相のようである.
万全を期して不具合が発生しないようにしていても,このように意外な落とし穴があるものである.
注意しなければいけない落とし穴は,修理品のライン復帰,抜き取り検査品の戻し先間違い,など見落としがちなところに潜んでいる物である.
別のお客様からも違う機種が混入していたというクレームをいただいた事がある.
この時は我々の製品の中に,別の会社の製品が混入していたというクレームであった.
返却いただいた製品を見ると,お客様が我々の製品のセカンドソースとして購入しているコンペチターの製品であった.そのセカンドソースの生産工場は車で20分ほど離れた場所にあり,混入するはずがない.
どう考えてもお客様倉庫で混入したとしか考えられない.
「お客様は神様です」というが,神様もたまには間違いをするようである.
変革リーダを探せ
中国の工場で生産の方法を変えたり,組織を変えたりするのがなかなかうまく行かないことがある.リーダ層や作業員の抵抗にあう.
日本の工場でも同様だが,多くの人は「今までのやり方」を変えることに抵抗がある.これは人類共通の特性ではなかろうか.いやひょっとすると生物共通の特性かもしれない.
ぬるま湯に浸かった蛙は徐々に水温が上がっているのに気がつかずついには茹で死んでしまう.
早く温度の変化に気がついて,危機感を持つリーダがいないことには組織もぬるま湯に浸かったまま茹で死んでしまうだろう.
経営者が危機感を持っていても現場がなかなか変革についてこない.現場が抵抗勢力になってしまう.しばしばこういう局面に出会う.
現場で変革を推進なければならないリーダが抵抗勢力側に入ってしまう.
無理もない.現場のリーダは「現在のオペレーション」をきちんと推進できる能力を評価されリーダの役割を担っているはずだ.
往々にして現状に満足しない人たちは,職場での評価が低く,埋もれていることがある.しかしこういう現状に満足しない人が「変革リーダ」としての役割を果たすことがある.
工場の中で改善活動をしていると,「現状リーダ」と「変革リーダ」の違いがよく見えてくる.
「現状リーダ」をすぐに「変革リーダ」に変えることはかなり難しい.
「現状リーダ」に変革マインドを埋め込む.変革マインドを持った人にリーダマインドを埋め込む.
いずれにせよ「変革リーダ」を見つけ養成するのは現場の活動を通してでなくては達成できないと考えている.
設計不良
製品の品質は設計段階でほぼ決まってしまうといっても過言では無かろう.
商品企画,設計段階で筋の悪い製品は,どんなに工場が努力しても品質はよくならないものだ.
従って,設計段階での品質の造り込み・レビューが重要である.
あるメーカの中国工場を指導していて驚いた事がある.
半完成品の最初の通電検査で不良が大量に発生しているのである.数%というオーダーではなく数十%も不良になっている.
訳を聞いて更に驚いた.
回路に使用しているICのばらつきによって,このようなことはしばしば起きる.
その場合検査外れ品は回路中の抵抗を交換してやれば検査は合格し良品となる.
従って工程内に山ほどラインアウトされた半完成品は,後ほど作業者が抵抗を交換してラインに再投入するのである.
私に言わせれば,これは設計不良である.
このような製品はすぐにラインを止めて,設計を変更すべきである.
しかしこの製品は量産開始以来ずっと工場の努力で生産し続けてきたのである.
今更差し戻されても,というのが本社設計部門のいいわけである.
ここは100歩譲って,先にICの特性を測っておきランク別にしておく.出庫するICのランクにあわせて抵抗を変更して生産する.このように部品表と製造基準を変えてもらった.
これで不良は1%未満となり通常の生産が可能となった.
更にこの工場には,試作審査と量産移行審査の制度を導入させた.
試作時の生産性の問題を整理し,これがきちんと解決していなければ量産には移らない.これをこの2回の審査できちんと確認をしてゆくわけである.
審査を通らなければ,本社の設計部門に差し戻しである.
この制度を導入して一番喜んだのが,工場サイドのエンジニアだった.彼らは毎回本社設計部門の言われるがままに生産するしかなかった.それが自分たちで審査をしてだめなら「設計を受け取らない」「作らない」という選択があることを知り,モチベーションがすごく上がった.
もちろん「作らない」という負の対応ばかりではなく,今まで押し付けられていた生産を,自分たちで改善するという意欲が出てきた.
このように製造現場が変わると,本社設計部門も必然的に変わらなければならなくなる.現場の改革が,連鎖して全社を改革してゆくのである.
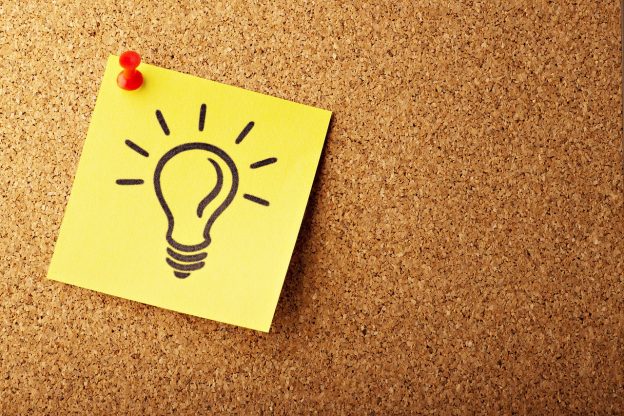
ポカよけ ダブルチェック
2007年11月4日付け朝日新聞にこんなユースが載っていた。
「スカイマーク機、着陸時にカートが動いて客が足を骨折」
3日午後7時15分ごろ、スカイマークの神戸発羽田行きボーイング767―300型機が着陸時、飲み物用のカートが動いて乗客2人にぶつかった。44歳の男性は右足の骨が折れる重傷で、47歳の男性も左肩に軽いけが。東京空港署が業務上過失傷害の疑いで捜査するとともに、国土交通省航空・鉄道事故調査委員会も4日、調査官2人を派遣する。
怪我人の内の一人は足を骨折しており、かなり重傷である。この記事だけでは何が原因か不明なので今回の事故に関しては言及しないことにする。
飛行機に乗ると、乗客の搭乗完了時搭乗口を閉める時に「乗務員はオートモードに切り替えた後、相互に確認を行ってください」という機内放送を聴くはずである。この後クルーが扉の操作を行った後、お互いに親指を立てあっているのをご覧になった事があると思う。
旅客機は乗降口を開けると自動的に非常脱出用の滑り台が出て来る様になっている。しかし空港で乗客が乗り降りする時にも滑り台が出てきてしまっては不都合なので、マニュアルモードにして扉だけ開けるわけである。
このマニュアル・オートモードの切り替えを万が一忘れてしまうと大変なことになる。
そのため「ポカよけ」と「ダブルチェック」を操作に仕込んである。
この操作でのポカよけは、モード切替の操作が完了しないと扉開閉のハンドルが操作できないようにしてある仕掛けのことである。扉が開いている時にマジックテープのたすきが扉開閉ハンドルにかかっている。このたすきをはずさないとハンドルは操作できない。このたすきにモード切替レバーの固定ピンが付いており、一連の操作で「うっかりミス」を防ぐ様になっている。
操作の後乗務員が別の扉がきちんとマニュアルモードになっていることをダブルチェックする。
搭乗口を閉める作業にこれだけの「ポカよけ」と「ダブルチェック」が仕込まれているのである。
飲食物用カートの固定がどのような「ポカよけ」「ダブルチェック」の仕掛けをしてあるのかは良く知らないが、乗降口のモード切替のように厳重ではなさそうである。
製造現場でも同様に「ポカよけ」「ダブルチェック」を組み込まないといけない工程がある。
皆さんの工場ではどんな工夫をされているだろうか?
このコラムは、2007年11月5日に配信したメールマガジン【中国生産現場から品質改善・経営革新】第6号に掲載した記事です。
【中国生産現場から品質改善・経営革新】は毎週月曜日に配信している無料メールマガジンです。ご興味がおありの方はこちら↓から配信登録出来ます。
【中国生産現場から品質改善・経営革新】
十点法
「十点法」という言い方をご存知だろうか.
あまりいい名前ではないが,部品の定量投入によるポカよけの一種である.
例えばネジ締め作業で必要なネジの数だけ作業前に取り置き,作業が終わったときにネジを過不足なく使用したことを確認するわけである.これによりネジの閉め忘れとか,製品の中への落下などを防止するわけである.
すなわち10点部品を使うならば,10個の部品を投入するという意味で「十点法」と言う命名になっている.
中国の工場で指導をしていた時に,製品組立工程でネジを5本締め付ける工程があった.このとき現場の組長さんに「このネジが一本足りなくなったらどうする?」と聞いてみた.
この組長さんは大変聡明な子ですぐに小皿を持ってきて,作業者に作業前にネジを必要数準備してから作業をするよう指示をしていた.
普通の組長さんだと,次の工程にネジの数を数える検査を追加したりする.
この方法でもネジの締め忘れがないことを保証できるかもしれないが,製品の中にネジが落下したのは検査できない.
それよりも,付加価値を生まない作業を増やしていることになる.
検査を追加することよりも,作業で品質を保証する仕組みを考えるべきだ.
製品に貼り付けるラベルを貼り忘れ,出荷先で見つかってしまった事がある.
この手の不良は厄介である.客先に出荷してしまった製品の選別検査,社内の完成品の再検査など,後向きの作業が大量に発生する.
客先にも改善対策を提示しなければならない.
当然工程内には外観検査があり,ラベルが貼ってあることも検査している.作業者がうっかり貼り忘れ,検査者もうっかり見逃したわけである.
うっかりの二乗なので,確率はかなり低いはずであるが往々にしてこういう事故はある.
殆ど不良が発生しないと,検査者の感度は落ちてしまうのであろう.
こういうときに「十点法」が活用できる.
ラベルを梱包単位に準備し,ラベルを使い切ったらラベルシールの台紙をベルトコンベアに載せる.梱包作業者はラベルシールの台紙が流れてきたら,梱包箱が一箱完成しているのを確認する.
ラベルを貼りそこなった場合の対処方法など,一工夫する必要はあるが,この方法はそれほど工数をかけずに,ラベルの貼り忘れがないことを保証できる.
同時に梱包数量の確認も出来ている.
読者の皆様の工場でも,同じような方法で改善できる事例がないだろうか.
ラインを止めなさい
「停線!(ting2 xian4)」
以前指導していた電気製品の組立工場で,しょっちゅう大声でこういっていた.日本語で言えば「ラインを止めろ!」という意味だ.
ベルトコンベアの流れ作業で,何か小さな問題が発生してもなかなかラインを止めない.現場の班長さんたちは,ラインを止めないで何とか修復しようと必死になっている.
彼らには「生産量のプレッシャー」があるのでなかなかラインを止めたがらない.ラインを止めるのは「悪」だと思っていたりする.
例えば,半田槽を出てきたプリント基板アッセンブリィの半田手直し工程で,作業が追いつかず手直し待ちの半製品があふれてしまっている.
こんな状況で,現場の班長さんは作業者の後ろで一生懸命作業者をせかしている.または自分で手直し作業を手伝って何とかしようとしている.黙って見ている班長さんなどは論外だ.
こんな時に「停線!」と大きな声を出すわけだ.
こういう状況で作業者をせかして仕事をさせれば,後工程の半田目視検査やICT検査で不良が増加する.そしてその不良品は修理されてまた半田手直し工程に再投入されるからますます物は滞留する.悪循環だ.
こういう状況ではまずラインを止めて作業が追いつかない原因を除去しなければならない.
半田槽の調整が悪く半田不良が多発しているので,手直しが増えている.
部品が浮いてしまったり,傾いてしまうために,手直しが増えている.
等,原因が必ずあるはずである.
この原因を除去した上でコンベアを再稼動する.
ラインを止めずに生産を継続する方が生産のロスは大きいはずだ.
ラインを止めるのが早ければ早いほど,生産のロスは減る.何よりも品質不良のリスクを少なくする事が出来る.
班長さんたちにはラインを止める勇気を持てというのだが,なかなか出来ない.
ラインを止めることにより,問題点をその場で改善するという習慣を身につけるべきだ.
特に設備で物を作っている場合など,多少の不出来は後で手直しすればよいと考え,そのまま作ってしまうことはないだろうか.
先日訪問したアルミダイキャストの工場は,原材料にアルミのインゴットを投入することはまれであった.殆ど不良品を鋳潰した再生材料で足りてしまっている.
実はこういう工場のほうが好きである.簡単に改善して差し上げられる(笑)
作業員は先生です
良く指導先の現場で「作業員は先生です」といっている.
ほとんどの場合通訳が意味が分からずぽかんと私の顔を見ている.または全然違う意味のことを言っている.従ってここだけは自分で中国語で言わなければならない.
無理もない,中国の工場ではほとんどの作業員は中学しか卒業してなくて都会に出稼ぎに来ているのである.中にはちゃんと中学も卒業していない子も混じっている.それを「先生だ」というのだから通訳も「!?」となってしまうのも無理はなかろう.
作業員は毎日何千回も何万回も同じ作業を繰り返している.それなりに効率のよい方法を編み出しているものだ.作業者の動作をじっと見ることにより,改善するべきところが見えてくる.
作業者は何も言わないけれど,問題点や,改善すべき点を教えてくれているのである.
現場のリーダは作業者の動作を,白紙の心でじっと見て勉強すべきである.
現場リーダの中には心得違いをしている者がおり,作業者を従わせるのが仕事だと思っている.本当の仕事は,作業者が仕事をやりやすく(生産効率の改善)することだ.
標準外作業で不良が出ると,対策書に「作業者に標準作業を教育しました」という回答が書いてある事がよくある.
作業者が標準作業を出来ないのには理由がある.
1.標準作業を知らない
2.標準作業を知っているが,うっかりした
3.標準作業がやりにくい
作業者の動作をよく見て,本当の原因を作業者から「目で聞く」ことが必要だ.
それぞれの理由に対して,対策が違ってくるはずである.
読者の皆さんは,ご自分の工場の状況に合わせてどんな対策が必要なのか考えてみてください.
セミナーのご案内
3月から毎月一テーマ,中国華南地区二会場で「品質改善・経営革新セミナー」を開催しております.
今までのセミナーの内容はこちらをご覧ください.
「品質改善・経営革新セミナー」
8月はこんな内容です.
■2007年8月度「品質改善・経営革新セミナー」
講演テーマ: 「工場監査で受注拡大,品質安定」
今回のセミナーはこんな方に聞いていただきたいと思います.
★お客様の工場監査が鬱陶しいという方.
お客様の監査は,工場を良く理解していただくチャンスです.お客様に安心いただいて受注を伸ばしましょう.
★協力工場・仕入先のQCDに不満を持っておられる方.
協力工場・仕入先の監査で安心できる工場を選定しましょう.又工場監査は協力工場・仕入先指導の絶好のチャンスです.
★中国工場のQCDに不満をお持ちのバイヤーの方.
安さに飛びついて中国工場から買い付けているが,200%全数検査(全数受け入れ検査,検品会社への委託)のコストを余分に払っていませんか?検査では品質はよくなりません.適切な指導が必要です.
日系の中堅から大手企業まで十数社,欧米・台湾・韓国の優良企業十数社,合計三十社以上の会社に,中国の工場に来ていただき工場監査を受けたことがあります.
協力工場や部材の仕入先工場はもっと多くの工場監査をしてきました.
その経験から分かったことは
★お客様に工場監査で安心していただければ,もっと注文がいただけること.そのためにどう準備し,どう説明するか.
★協力工場や部材仕入先の監査で安心できれば,品質はよくなること.そのためにどう監査し,指導しなければならないか.
今回はその内容を皆様に公開いたします.
お客様の工場監査はチャンスです.工場は優秀な営業マンです.
工場に営業活動をさせて受注を拡大しましょう.
品質改善は源流管理が重要です.協力工場の工場監査で品質改善・安定を狙いましょう.
スケジュール:
8月01日(水) 深圳会場 明華国際会議中心 明昌庁
8月08日(水) 東莞会場 東莞・世博商務酒店 3F会議室
時間: 15:00~17:00 受付14:30開始(各会場共通)
お申し込みはクオリティマインドホームページからお願いします.