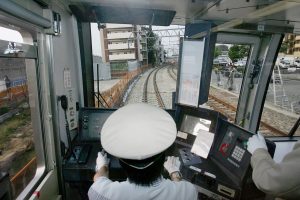
時事通信社
4月11日に配信したメルマガ第652号「組織事故」で福知山線脱線事故は組織事故の一つだったとご紹介した。
運輸安全委員会は、福知山線脱線事故の調査報告書を発行している。
全261ページ+別添資料の膨大な報告書だ。
簡単にまとめると以下のようになる。
原因:
本件運転士のブレーキ使用が遅れたため、本件列車が半径304mの右曲線に制限速度70km/hを大幅に超える約116km/hで進入し、1両目が左へ転倒する様に脱線し、続いて2両目から5両目が脱線したことによるものと推定される。
以上の原因は、脱線に至る物理的原因だ。運転士のブレーキ操作が遅れた誘引があるはずだ。
誘引:
事故発生前に伊丹駅で停止位置を通過してしまい、車掌が非常ブレーキをかけ停止位置に後退して停車している。運転士はこのミスを内緒にしておいて欲しいと車掌に車内電話で頼んでいる。
本件運転士は2004年6月に片町線下狛駅で所定停止位置行き過ぎ事故で13日間の「日勤教育」を受けている。日勤教育とは、重大インシデント、規約違反、ヒヤリハット事象を起こした者が受ける教育で数日から一月以上続くケースもある。懲罰的な要素が強い教育指導だ。本件運転士は日勤教育を避ける事に気をとらわれブレーキをかけるのが遅れている。
日勤教育には、事故またはヒヤリハットが発生した原因を分析する事が含まれているというが、本件運転士の日勤教育の記録を見ると指導官との指導問答、感想文のような本人レポートしか残っていない。
この脱線事故を組織事故としたのはここにある。
日勤教育を受けている間は、同僚運転士の目にさらされる事になる。
教育指導というより、数日間も説教を聞かされているだけ。
これではヒヤリハットや失敗を隠蔽する風習が組織にはびこり、ヒヤリハット事例で問題の未然防止どころか再発防止さえおぼつかなくなる。
ヒヤリハットや失敗を責任追及すれば、問題は隠蔽され必ず再発する。
ヒヤリハットや失敗を共有すれば、発生原因を分析し再発対策が可能となる。
失敗を称賛する必要はないが、失敗を学びに変え、再発対策、未然対策を称賛する組織文化を持つべきだと思う。
永田町の役人、旧国鉄、旧財閥系企業など古い因習があり、変わる事が難しいとは思うが、変わらねば恐竜やマンモスの様に死滅してしまうだろう。
このコラムは、2018年5月2日に配信したメールマガジン【中国生産現場から品質改善・経営革新】第661号に掲載した記事です。
【中国生産現場から品質改善・経営革新】は毎週月・水・金曜日に配信している無料メールマガジンです。ご興味がおありの方はこちら↓から配信登録出来ます。
【中国生産現場から品質改善・経営革新】